- Home
- Case Studies
- Soft drink bottler in novosibirsk operates without ppm
Industry
Soft drink bottling industry
Challenge
Need to eliminate the use of Potassium Permanganate (PPM) due to its dangers and environmental impact
Solution
Implementation of Pentair Union Engineering CO2 Combustion Based Unit
Results
Improved CO2 quality, reduced MEA usage, significant savings on OPEX, and a more sustainable CO2 purification process
Large soft drink bottler in Novosibirsk upgraded to greener technology
Situated on the banks of the River Ob and with the beautiful Golden Mountains of Altai as neighbor lies the third-largest city in Russia; Novosibirsk (the new city in Siberia). Despite its just 123 years of age, 1.567.087 people are living here, 3335 km from Moscow with the Trans -Siberian railway. Our customer, a leading soft drink bottler opened this production back in 1996 and today supplies some 12 mil people.
To continue improvement of the production the CO2 plant was upgraded to a Potassium Permanganate (PPM) free CO2 solution.
“A Potassium Permanganate (PPM) Scrubber “does the job”, but there are also some challenges.”
Long cooperation with the customer
Pentair Union Engineering has a long history of cooperation with this customer worldwide – this is also the case in Russia. The CO2 plant in Novosibirsk came into production back in 1998. A traditional self-generating plant (Combustion-based type) prepared for a 750 kg/h production. Like most plants from that time, it was delivered with a Potassium Permanganate (PPM) Scrubber to remove challenging impurities from the CO2. This is a well-proven and efficient solution that “does the job”, but there are also some challenges when using the chemical – we will get back to that.
Why remove the use of PPM? Well, there are several answers to that. One reason could be that replacing the quality check of the PPM is indeed a manual process, something you need to keep an eye on a daily basis and if not changed in due time it will influence the purity of the end-product.
PPM is considered dangerous, it is on the UN’s list of “Chemicals used in the manufacture of narcotic drugs and explosives”, and it is further harmful to the environment.
A difficult chemical
Over time, the demands for handling the chemical have been intensified and it is both difficult to buy, to use in operation, and difficult to dispose of. In some regions of the world, it is finally becoming forbidden to use the chemical.
To sum it up PPM is:
- Difficult to import
- Expensive to transport
- Hard to dispose of correctly
- Dangerous to handle and store (hazardous, explosive, and risk of spontaneous combustion)
- An element that affects your company’s overall environmental contribution negatively
The bottler in Novosibirsk decided to focus on an environmentally conscious solution that will remove the use of critical chemicals and insure identical high product quality, with the installation of this new plant upgrade.
The customer in Novosibirsk has taken this step because the legislation regarding disposing of the used PPM has over the years been toughened up and it is not only difficult but also a very expensive maneuver to handle the chemical. By upgrading, they avoid the difficult process it is to use and dispose of PPM and eliminate the risk of being fined if the chemical is handled wrong, and at the same time they obtain a more sustainable CO2 purification.
“PPM is considered dangerous and it is on the UN’s list of dangerous chemicals.”
Less MEA usage and saved OPEX
The solution was to install an additional adsorption filter with a special grade adsorbent capable of removing critical impurities to the same extent as the existing scrubber. The filter was designed to be regenerable to avoid frequent replacement of the filling and being fully automatically operated. The new upgrade involves no maintenance on a weekly basis.
The new filter was fully integrated into the existing controls and HMI of the plant for easy access to the operating state and data for the operator.
The filter-upgrade implemented has worked perfectly and the operators, who continuously monitor the CO2 product quality by a sophisticated inline analyzer system (Carboscan 150), capable of detecting a broad array of impurities, are reporting that the CO2 quality since the installation of the filter has even improved.
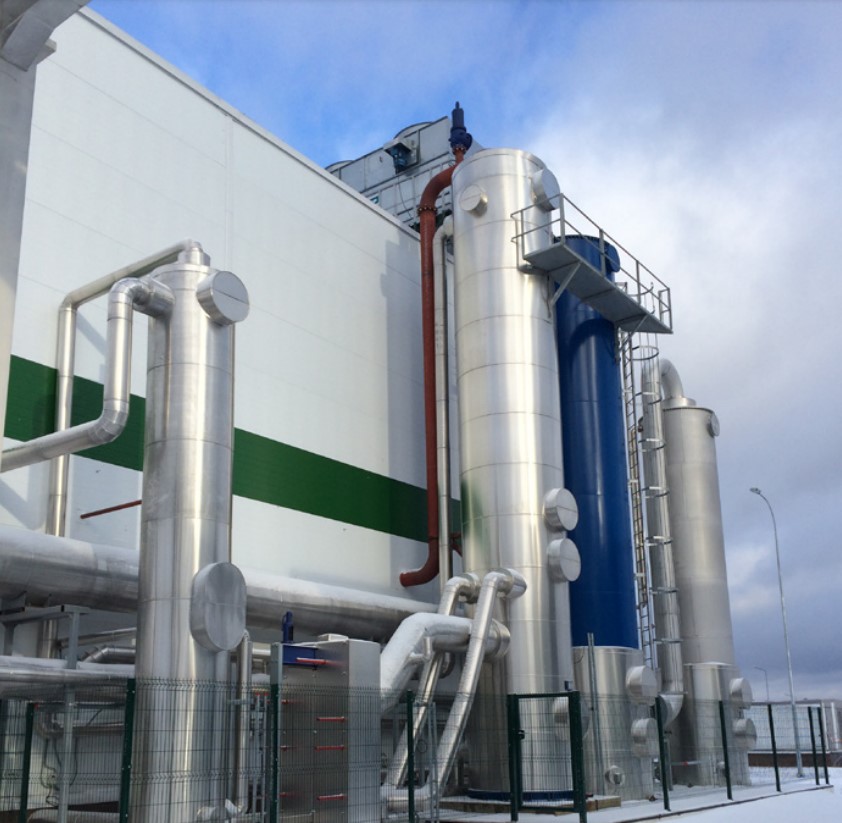
CBU plants delivered from Pentair Union Engineering are since 2006 by default equipped with a Union patented NOxFlash technology that replaces the traditional use of PPM. Besides the obvious advantages of not using PPM this solution also offers a reduced MEA consumption and significant savings on OPEX.
This highly efficient purification technology is, however not easily integrated into existing plants using PPM, so here a filter upgrade can be a very big step toward smoothing the day-to-day operation.
RELATED PRODUCTS
Union Engineering CO2 Self-generating Plants - Combustion Based Unit - CBU
Based on the latest technologies, CO2 generating plants (CBU) from Union Engineering meet the strictest CO2 quality requirements.