- Home
- Case Studies
- Greene king
Industry
Brewing Industry
Challenge
Need to modernize filtration and stabilization systems to improve reliability and reduce beer losses.
Solution
Implementation of Pentair Beer Membrane Filtration (BMF) Technology.
Results
Substantially reduced beer losses, improved product quality, increased flexibility in brewing volumes, and enhanced reliability for packaging partners.
BLENDING THE OLD WITH THE NEW
HOW GREENE KING BREWERY ADAPTED WHEN NEEDED
As befits a brewer that traces its origins to 1799, Greene King Brewery is skilled in the art of blending the old and established with the new and innovative. Nowhere is this truer than at its Westgate brewery, with tried and trusted machinery and methods retained alongside installations of the latest technologies.
This traditional English brewer is situated on a 74-acre site on the west side of the sleepy county town of Bury St Edmunds, in rural West Suffolk. The Westgate site boasts a 600,000-barrel or 980,000 hectolitre (hl) capacity, with virtually all of its output consisting of ales. Its leading brands include Old Speckled Hen, Ruddles, Abbot Ale and the increasingly export-driven Greene King IPA.
Greene King Head of Production Strategy, Ross O’Hara, commented: “Our malting plant dates back as far as 1938 and continues to perform well. Surprisingly, other parts of our brewery originally installed in the 1990s now contain outdated software systems which create operational ‘hiccups’ in our process.”
There was also a change of ownership at Greene King. Hong Kong-based CK Asset Holdings (CKA) acquired the brewing operations and more than 2,700 Greene King pubs and restaurants in August 2019. The company was also receptive to funding necessary upgrades at Westgate.
BEER LOSSES SUBSTANTIALLY REDUCED
Something making life easier for Greene King’s brewing team is the presence of Pentair Beer Membrane Filtration (BMF) Technology. In 2019, Pentair was chosen to replace an aged kieselguhr-based primary filtration system. Three BMF +FLUX Smart Compact Units were installed, each rated at 80hl/l, providing gains in reliability and consistency while reducing beer loss. Pentair BMF System was put to the test during COVID-19 induced lockdowns throughout 2020 and into 2021. With pubs and on-trade closed across the UK for the better part of a year, demand for beer was instead met by bottled and canned products.
“The filters have been used harder and harder,” said O’Hara. “To be honest, if we didn’t have that system, I think we would have struggled to meet demand.
THE NEXT STEP: STABILIZATION MODERNIZATION
During this period of heightened demand, Greene King, unable to count on the performance of its regenerative polyvinylpolypyrrolidone (PVPP) system, resorted in the short term to expensive, single-use PVPP to ensure reliability. But there remained an issue with beer stabilization. Greene King was working an aged PVPP system that, on average, was costing up to 26 hours a week due to either planned stops or frequent breakdowns. The result was a constant need to recover and reprocess the beer.
Greene King returned to technology it trusted, purchasing two 160 hl/h Pentair BeerStab Units. The capacity was configured so that the output from two BMF units could be sent to a single BeerStab Unit, creating flexibility on regeneration and clean-in-place (CIP) operations of the other units. It also allowed for flexibility on Greene King’s brewing schedules. The brewer boasts a large and diverse brand portfolio. Average weekly production is 9,500 barrels (15,500hl), comprised of twenty brews of sometimes more than ten different beers, with everything brewed at sales gravity.
FLEXIBILITY ON BREWING VOLUMES A KEY BENEFIT
Production runs can be as low as the minimum brew length of 50 hl–this from Westgate’s in-house St Edmund Innovation Brewery–or considerably more for other brands such as Old Speckled Hen.
The BMF and BeerStab Units are located side-by-side in the brewery, integrated as a single unit. The shorter lengths of pipe linking the units mean less priming is required, further reducing beer losses. Operation is simple, requiring just a single operator who only needs to enter what type of beer needs to be filtered, whether continuous or batch, and the desired flow rate. All of the subroutines are automated, eliminating any need to modify or tweak the operation.
Greene King differs from the industry norm in how it measures beer filtration. Instead of considering the whole polyphenol load, its preferred measurement is the level of tannoids, the haze forming polyphenols. It aims to have less than 25mg of tannoids per liter of beer. “We used to get sporadic failures with the old PVPP, and we would need to refilter,” says O’Hara. “We haven’t had to refilter since we put the BeerStab in–it’s spot on!”
“That was the huge part for us, getting something that could do the large-scale batches,” O’Hara commented. “To find a solution that could be efficient and give us 50 hl with minimal losses and that could also do three to four thousand hectolitres without stopping. There was no other solution that we found could do that apart from the Pentair BMF & BeerStab combo.”
- Ross O’Hara, Head of Production Strategy at Greene King Brewery
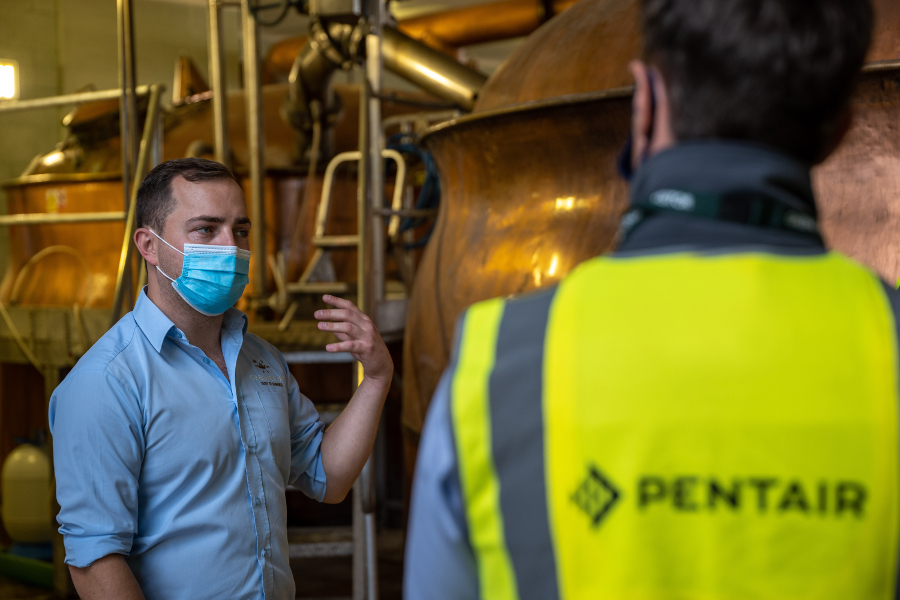
RELIABILITY FOR PACKAGING PARTNERS NO LONGER A PROBLEM
The reliability of the Pentair BMF and BeerStab units has had positive implications for packaging in bottles and cans. Both packaging lines are remote from the brewery, requiring finished beer to be delivered by tanker. Under the old PVPP stabilization regime, tankers could be waiting for hours until breakdowns were fixed. The filtration and stabilization process at Westgate is no longer the brewery’s limiting point. In addition, the Brewery is leveraging remote monitoring and access to the Unit Software by Pentair Engineers as needed. A Pentair Team based in the Netherlands monitors functionality for faster resolution if issues arise, helping to ensure reliability. Greene King is also benefiting from a Pentair Leasing Option, where it pays a set fee for each hl of beer processed by the filtration system. The arrangement allows for reduced capital expenditure, with Greene King having purchased the hardware and software but not the membranes. O’Hara notes, “We know per hectolitre what the cost is, and then we can put that into the price of the beer. It is pennies. In terms of company overheads on a batch of beer, it hardly blips on the system.”
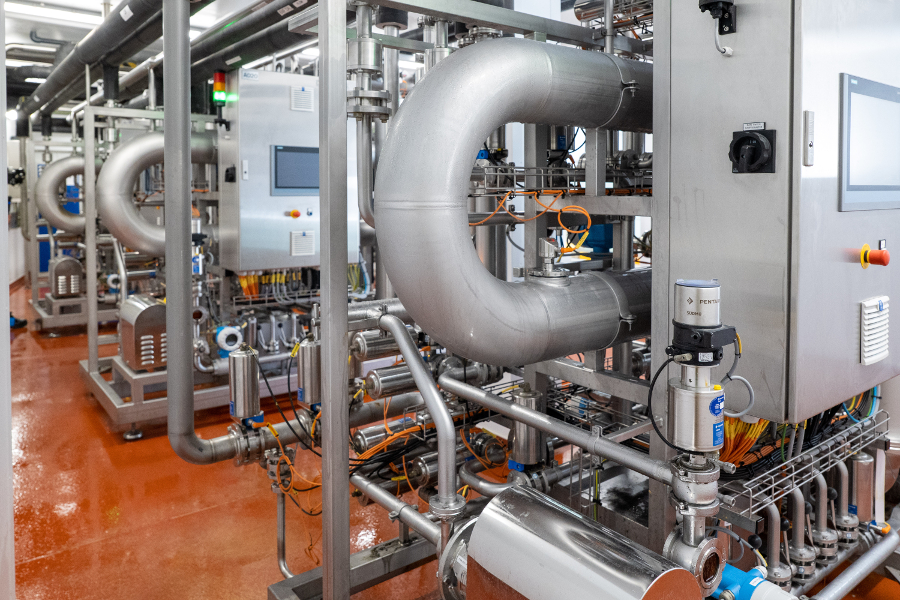
FLEXIBILITY FOR THE SHORT AND LONG-TERM FUTURE
The future is unknown, with any number of scenarios possible in the world inhabited by brewers. Greene King is pleased with the flexibility provided by Pentair BMF and Pentair BeerStab to meet any number of production requirements. Should there be a sudden or seasonal increase in demand, all three BMF units can run in batch mode to push through extra beer volumes. And as demand for Greene King brands increases, one day necessitating additional capacity requirements, Pentair’s modular approach makes expansion of its filtration and stabilization requirements easy.
“It’s certainly future-proofed,” says O’Hara. “Because it is a modular system, we can just add a fourth skid – or even a fifth skid.” “Pentair really took the time to understand our needs and gave us a bespoke solution,” continues O’Hara, “They didn’t tie us down with limited A, B or C options.” Greene King also found it refreshing to work with a technology provider that served up a special blend of expertise. “And there’s the enthusiasm of their sales team. They are all keen brewers, meshing the two worlds of brewing and engineering together,” notes O’Hara, “I’ve not come across that before in an organization the size of Pentair.” What is next for Greene King? There is a five-year investment plan being developed to secure the business continuity and environmental performance of Westgate.
Brewed Perfection at Greene King Brewery, UK
Learn how Pentair equipped Greene King with a smart beer membrane filtration system and Südmo process valves, helping the brewery to drive greater process efficiencies.
Related Products
Beer Membrane Filtration System for small and craft breweries that produce at a capacity between 30-80 hl/hr.
Turnkey filtration solution for breweries with capacity 7,000–22,000 hl/d.
Beer Membrane Filtration System for large breweries that produce at a capacity between 200-900 hl/hr.