- Home
- Case Studies
- Deschutes
Location
Bend, Oregon, USA
Start-up
July 2017
Source
Brewery wastewater
Application
Wastewater reuse
Technology
AnMBR100-140 l/d
background
With the growing popularity of craft brews and demand for its special beers, Deschutes Brewery in Oregon, USA, is planning to step up production. The company takes sustainability very seriously. Economics, regulations and space limitations determined the choice to pilot Pentair’s AnMBR technology to treat the brewery’s wastewater and produce biogas in the process.
Deschutes Brewery was founded in 1988 in a public house in the town of Bend in Central Oregon. The new brewery became well-known for its Black Butte Porter and never looked back since. It now produces many new flavors and brews, such as Mirror Pond Pale Ale and Fresh Squeezed IPA. The company was among the first to ride the wave of returning interest in traditional ales and porters. The reviving beer culture is being cherished in the U.S. The number of ‘craft brewers’, producing less than six million barrels a year, has grown from a few dozen in the 1980s to over 6,000 today.
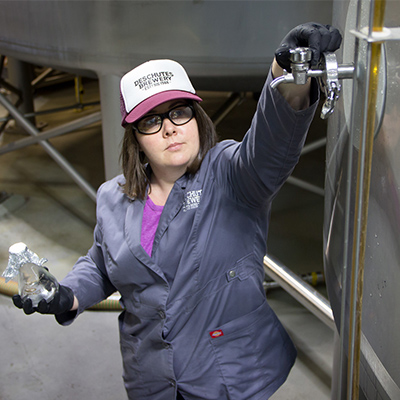
Three decades after its humble beginnings, Deschutes Brewery is still family and employee owned. Ranked by sales volume, it is now the eighth largest craft brewery in the USA. The company is dedicated to core values of authenticity, quality and responsibility. Water and land conservation are important focal points.
Deschutes is planning to build a new brewery in Virginia on the east coast in coming years. Meanwhile the main brewery in Oregon has to increase production while complying with environmental law and protecting natural resources.
brewery wastewater
Brewing involves a lot of water. The process, even without considering crop irrigation, takes at least three gallons of water for every liter of beer. In a craft brewery, this typically more than doubles. With the increasing worldwide strain on water resources, all brewers are forced to explore how to do more with less water. Brewery wastewater mostly contains spent grains from the malting and lautering steps. Traditionally, the spent grains are trucked off to a landfill, while the watery parts go to a public wastewater plant.
With growing production levels, the waste streams become a more pressing problem. Deschutes main brewing facility in Oregon is already discharging a billion gallons of treated wastewater on the Deschutes River every year. Expanding production would mean increasing that amount, along with the space needed to treat the wastewater. And while treating such nutrient-rich wastewater presents an obvious opportunity to produce more biogas, Deschutes needs to consider the reliability of such a process, as well as the available space.
the promise of anmbr
Faced with escalating sewer surcharges and space limitations, the brewery recognized the need to further explore its on-site wastewater treatment options. Deschutes decided to evaluate anaerobic membrane bioreactor (AnMBR) technology, given its ability to accommodate high levels of COD and TSS while consistently producing a high-quality effluent and maximizing biogas production.
The AnMBR features a bioreactor that excludes oxygen from the process. The advantages compared to an oxygenated process are plentiful.
The COD reduction rates typically reach over 98 percent and there is no need to develop granular sludge. The process is very robust and can handle large variations in feed composition, even with high levels of FOG or salinity. All biomass is used, eliminating waste while maximizing energy production. And last but not least: the effluent is of such quality that it can be reused for cleaning purposes immediately.
The Pentair ANMBR Design
Pentair’s decades of experience with membrane technology have led to highly reliable AnMBR designs. Submerged membrane units have been abandoned in favor of external installation, making it easy to inspect, clean, and maintain the membranes. The bioreactor thus never needs to be opened, which goes a long way in solving odor issues. X-Flow tubular membranes are used for the solids-liquid separation step, providing an effluent without TSS and retaining all of the biomass inside the bioreactor.
In July 2017, Deschutes initiated a pilot study to verify that Pentair’s AnMBR technology is capable of handling the levels of COD and TSS created by spent hops and yeast residuals. The pilot also served to identify the organic loading rate, the MLSS concentration, and ideal sludge retention time to minimize the footprint without sacrificing effluent quality and membrane performance. Before designing the ideal full-scale system for the Deschutes Brewery, the team had to determine the membrane flux rate, crossflow velocity, filtration cycle, backwash interval, and chemical cleaning frequency.
The six-month pilot showed the system’s superior performance to the brewery’s utility staff, who also learned about the operational ins and outs. The ability to accommodate the variable and high-strength wastewaters typically generated by craft breweries was clearly demonstrated. With fouling issues firmly under control due to the external set-up and Helix flux enhancement, the membranes provide a durable and reliable barrier for many years of demanding operations. The almost absolute separation between solids and fluids keeps the biomass in the reactor and delivers a superior effluent quality. The pilot warrants the construction of a full-scale version and allows Deschutes to plan for future water reuse options.
results
parameter |
units | FEED | permeate | reduction rate |
COD | mg/L | 14,000 - 26,000 | 350-550 | > 97% |
TSS | mg/L | 3,500 - 6,000 | Non-detactable |
Related products
Treating high strength wastewater and producing high quality filtrate in bioreactor applications.